Керамический двигатель
В начале 1982 года в одной из телевизионных передач "Международная панорама" зрители увидели демонстрируемый японской фирмой "Киото керамике" и автомобилестроительной компанией "Исуд-зу" легковой автомобиль, приводимый в движение необычным двигателем. Этот двигатель мощностью 55 л. с, с рабочим объемом 2,8 л был сделан не из металла, а из керамики. Показали и изготовленные из керамических материалов его основные детали, на первый взгляд мало чем отличающиеся от таких же металлических. Это сообщение вызвало огромный интерес не только у специалистов, но и у широкого круга автолюбителей, что, в общем, неудивительно. Ведь речь шла о моторе, значительно более экономичном, чем двигатель внутреннего сгорания. А он, несмотря на далеко не идеальные экономические показатели, вот уже почти сто лет удерживает в автомобилестроении позицию лидера, хотя настойчивые попытки изменить эту традицию не прекращаются.
Первый автомобиль, как известно, был сконструирован и изготовлен на исходе прошлого века. В начале нашего столетия он уже приобрел все основные черты современной машины. Первые автомобильные двигатели, получившие широкое распространение, были четырехтактными бензиновыми с искровым зажиганием от магнето. Мощность двигателей внутреннего сгорания тогда не превышала 35 л. с, а степень сжатия была в редких случаях более 3. Дальнейшее развитие автомобилестроения характеризовалось повышением степени сжатия до 8-10, введением турбонаддува и расширением сферы применения дизелей, значительно более экономичных, чем бензиновые моторы с искровым зажиганием. Однако, несмотря на значительное совершенствование эксплуатационных свойств автомобильных двигателей внутреннего сгорания, особенно за последние 20-30 лет, основной их недостаток- низкую эффективность использования тепла - устранить не удавалось. И хотя теоретически в таких двигателях в полезную работу можно превратить около 70% энергии израсходованного топлива, на практике эффективный кпд обычно не превышает 28-38% Как бы мы ни совершенствовали процесс сгорания топлива в двигателе, основная масса выделившегося при этом тепла все равно будет теряться с охлаждающей водой, маслом и выхлопными газами. Причем больше всего тепловых потерь идет через систему охлаждения: до 40%- И это неизбежно, так как без охлаждения металлические детали двигателя не выдержат тепловых нагрузок, возникающих при его работе.
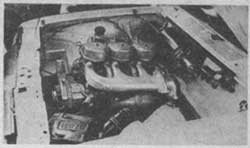
Керамический трехцилиндровый дизель, изготовленный фирмой "Киото керамике" и установленный на автомобиле фирмы "Исудзу".
Естественно, возникает вопрос, а нельзя ли повысить эффективность автомобильного двигателя, хотя бы за счет частичного использования тепловых потерь? Можно. И это делают на современных судах с дизельными силовыми установками: применяют систему глубокой утилизации тепла выхлопных газов, охлаждающей воды, масла и наддувочного воздуха после турбокомпрессора. В результате удается повысить кпд силовой установки до 50-60%. К сожалению, такой путь для автомобильного двигателя неприемлем, так как привел бы к существенному увеличению его массы и габаритов.
Вот и получается, что современный автомобильный двигатель обречен, по сути дела, больше греть окружающий воздух, чем совершать за счет полученного тепла механическую работу. Где же выход?
ПРОТИВОРЕЧИВАЯ СИТУАЦИЯ
Если на стенки камеры сгорания двигателя тонким слоем нанести теплоизолирующее покрытие, то удастся значительно снизить температуры поршня и гильзы цилиндра и тем самым уменьшить отвод тепла в охлаждающую воду. А что это дает с экономической точки зрения? Исследования показывают, что топливная экономичность двигателя при этом возрастает на 3-5%, а износ цилиндров уменьшается на 20-25%.
В соответствии с законами термодинамики для повышения кпд двигателя и его топливной экономичности необходимо увеличивать температуру цикла. Однако в этом случае поток тепла через стенки цилиндров возрастает, что приводит к увеличению потерь тепла в охлаждающую воду, а при их недостаточно эффективном охлаждении - к перегреву и снижению срока службы мотора.
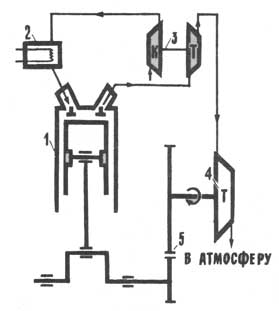
Принципиальная схема турбокомпаундного (комбинированного) дизеля марки TCPD-450 (фирма "Камминс"): 1 - керамический двигатель; 2 - воздухоохладитель; 3 - турбокомпрессор; 4 - силовая газовая турбина; 5 - зубчатая передача (редуктор).
Таким образом, ситуация противоречивая: с одной стороны, для повышения экономичности двигателя желательно иметь более высокую температуру деталей, образующих камеру сгорания; с другой стороны, для повышения надежности работы деталей их температура должна быть как можно ниже. Несоблюдение второго условия может привести к перегреву деталей, разрушению масляной пленки и возникновению режима сухого трения. Устранить это можно лишь более интенсивным охлаждением деталей цилиндра, что опять-таки увеличит потери тепла в систему охлаждения. Вырваться из этого круга, используя применяемые в настоящее время в двигателестроении материалы, не представляется возможным. А если улучшить механические свойства металла за счет введения специальных добавок, позволяющих деталям выдерживать более высокие температуры? Это, безусловно, даст положительный результат, но до конца задачу не решит.
Радикально проблема была бы решена, если бы удалось создать двигатель, вообще не нуждающийся в системе охлаждения и у которого между рабочими деталями и окружающей средой не происходил бы обмен тепла. На языке термодинамики это значило бы, что создан адиабатный двигатель.
Эту заманчивую идею и пытаются реализовать в керамическом двигателе.
РАДИКАЛЬНОЕ РЕШЕНИЕ
Способность керамики выдерживать высокие температуры давно привлекает внимание ученых и инженеров-двигателе-строителей. В практике дизелестроения уже не одно десятилетие для уменьшения перегрева деталей применяют теплоизолирующие покрытия поршней, в том числе и из керамических материалов. Такие покрытия наносят с помощью специальных плазменных установок, что обеспечивает прочное сцепление керамики с основным металлом. Толщина покрытий обычно не превышает 0,5-0,6 мм. Некоторые дизелестроительные фирмы, например, американская "Камминс", значительное время экспериментируют с поршнями и вставками из керамических материалов. Так чем же замечательны керамические материалы и что побудило специалистов попытаться перейти на них?
Детали двигателя, изготовленные из керамических материалов, в отличие от обычных (они работают при 250-450° С) могут выдерживать температуры до 1300- 1500°С. Благодаря высокой термостойкости и малой теплопроводности керамики отпадает необходимость в охлаждении отдельных деталей, а при изготовлении из керамических материалов всех деталей - и необходимость вообще в системе охлаждения. Кроме того, керамические изделия легче равнопрочных металлических. Так, по данным фирмы "Камминс", разрабатывающей свой вариант керамического двигателя, благодаря отсутствию системы охлаждения, а следовательно, и таких устройств, как водяной насос и радиатор, масса двигателя уменьшится на 20% по сравнению с традиционным агрегатом той же мощности.
Создание более высокой температуры цикла и устранение потерь тепла, связанных с охлаждением деталей, позволит поднять кпд двигателя до 45% и выше, значительно снизить расход топлива-по
результатам испытаний у керамического двигателя он был на 34% меньше, чем у традиционного той же размерности, то есть имеющего тот же рабочий объем цилиндров.
Весьма существенно, что повышение температуры деталей камеры сгорания двигателя (до 1200°С} ' делает керамический двигатель многотопливным. Это значит, что могут использоваться бензин, керосин, дизельное топливо, спирт, синтетические топлива из угля и горючих сланцев и при необходимости даже некоторые сорта мазута. Кроме того, благодаря более высокой температуре в камере сгорания значительно возрастет топливная экономичность двигателя при частичных нагрузках, что очень важно для транспорта, движущегося в условиях города. Благодаря более полному сгоранию топлива в цилиндрах снизится и уровень токсичности выхлопных газов.
Для деталей двигателя, работающих при высоких температурах (250-450° С) и подверженных большому износу, наиболее подходящими керамическими материалами следует считать карбиды и нитриды кремния. Сырьем для их получения служат широко распространенные в природе вещества: кварцевый песок, полевой шпат и каолин. Следовательно, при отработанной технологии изготовления деталей поршневого двигателя из керамики замена дорогостоящих легированных и жаростойких сталей положительно скажется на его стоимости.
Использование благоприятных свойств карбидов и нитридов кремния в технике стало возможным благодаря созданию технологии изготовления из них деталей требуемой формы путем горячего прессования или спекания основного материала с применением связующих веществ. Существенно, что керамический материал, получаемый по такой технологии, обрабатывать легче, и поэтому именно ему отдается предпочтение при изготовлении деталей двигателя.
Механические свойства керамики в значительной степени зависят от пористости: чем она меньше, тем выше показатели прочности. Следует отметить, что материал из нитрида кремния, несмотря на пористость (радиус пор обычно не превышает 0,2 мм), отличается значительной прочностью и чистотой поверхности. Для достижения высокой плотности в большинстве случаев в керамику вводят добавки, но они оказывают неблагоприятное воздействие на теплостойкость материала.
КОМБИНИРОВАННЫЙ ДВИГАТЕЛЬ
Тепловая изоляция некоторых деталей двигателя, например, поршня, покрытиями или изготовление их из керамических материалов способствует достижению более высокой температуры выхлопных газов. Благодаря этому тепловая энергия выпускных газов у двигателей с наддувом составляет уже 55-57% от полученной npji сгорании топлива, по сравнению с 30- 40% у дизелей без тепловой изоляции деталей цилиндра. Появляется возможность использовать такие энергоемкие выхлопные газы двигателя, заставив их совершать дополнительную работу, помимо привода турбокомпрессора.
Именно по такому пути и пошли специалисты фирмы "Камминс" при реализации проекта так называемого турбокомпаундного (комбинированного) транспортного дизеля повышенной мощности, созданного на базе серийного двигателя. Принцип работы комбинированного двигателя следующий. Выхлопные газы из цилиндра двигателя поступают в турбину турбокомпрессора, подающего в цилиндр двигателя воздух под давлением (0,5-2 кгс/см2). Пройдя эту турбину, выхлопные газы, температура которых еще достаточно высока (600-700°С), поступают в тяговую турбину, связанную редукторной передачей с коленчатым валом двигателя. Расчеты, а также последующие моторные испытания показали, что двигатель развивал на 17% большую мощность при более низком числе оборотов коленчатого вала (1900 вместо 2200 об/мин). Турбо-компаундный двигатель прошел 1000-часовые испытания на стенде и в составе тягача на 420-километровом испытательном участке. Результаты этих испытаний показали, что кпд двигателя повысился на 5%, а удельный расход топлива снизился на 12-15% по сравнению с серийным дизелем той же размерности.
Ресурс двигателя пока еще не превышает 250 часов. Основная причина быстрого выхода из строя деталей - низкие прочностные свойства применяемых керамических материалов. Однако, несмотря на это, специалисты фирмы в скором времени надеются приступить к постройке объединенного в одном агрегате керамического и турбокомгтаундного двигателя, что поз-
волит повысить эффективность первого. Мощность такого транспортного двигателя внутреннего сгорания составит около 640 л. с. при частоте вращения коленчатого вала 1900 об/мин; это приблизительно на 60% больше мощности серийно выпускаемого фирмой дизеля той же размерности. Как показали расчеты, кпд у нового Двигателя будет 48%. Предполагается, что устранение потерь тепла в охлаждающую жидкость и уменьшение потерь на трение позволит в будущем снизить удельный расход топлива на 55-60% по сравнению с современными автотранспортными двигателями. Конечно, ввиду высоких температур деталей цилиндро-поршневой группы придется вместо смазки их минеральным или синтетическим маслом применить газовую смазку; подшипники скольжения заменить на подшипники качения; направляющие клапанов, втулки коромысел и толкатели изготовлять из самосмазывающихся материалов.
РЕАЛЬНАЯ ПЕРСПЕКТИВА
Достоинства керамических материалов и выгоды, которые сулит их применение в двигателях внутреннего сгорания, несомненны.
Для организации серийного выпуска таких двигателей требуется серьезная перестройка производства, а следовательно, и значительное время. Но не это главное.
Сегодня работы над созданием керамического двигателя наряду с фирмой "Киото керамике" ведутся в США (фирмы "Камминс", "Форд"), в ФРГ ("Фольксваген"), в Италии (ФИАТ).
Испытания автомобильного керамического двигателя мощностью 50 л. с. фирмы "Фольксваген" дали приблизительно такие же результаты по надежности, что и у фирмы "Камминс".
У автомобильного двигателя "Петтер" серии AVB детали цилиндра безотказно проработали всего 53 часа. Правда, как показали результаты испытаний, детали, изготовленные из керамики на основе циркония, имели несколько больший срок службы, но все же недостаточный для нормальной эксплуатации двигателя.
Несколько лучшие результаты получены на одноцилиндровом керамическом двигателе мощностью 8 л. с. японской фирмы "Киото керамике". Двигатель, как сообщается, успешно прошел 500-часовые испытания. Что это: очередная реклама или результат решения проблемы повышения прочности деталей двигателя из керамики? Вполне возможно, что это всего-навсего следствие меньшей их нагруженности. Да и длительность испытаний не столь уж значительно превосходит срок службы керамических двигателей фирм "Камминс" и "Фольксваген".
Автомобильная компания "Исудзу" и фирма "Киото керамике" о продолжительности безотказной работы своего керамического двигателя не сообщали.
Можно ли ожидать, что в ближайшее время керамический двигатель завоюет мировой рынок? Скорее всего нет. Несмотря на достигнутые успехи в области создания более экономичного керамического двигателя, говорить о его серьезной конкуренции традиционным двигателям внутреннего сгорания еще рано. В современных двигателях применяются материалы, технология обработки которых доведена до совершенства, и благодаря массовому их выпуску себестоимость двигателя незначительная. Ресурс же деталей двигателя из керамических материалов мал, да и технология получения этих материалов и их обработки оставляет пока желать лучшего. Эти два обстоятельства, несмотря на заложенные в керамическом двигателе значительные преимущества, и служат пока серьезными препятствиями на пути его широкого распространения,